In various industries, liquid processing plays a critical role in the production and formulation of products. Whether it's food and beverage, pharmaceuticals, cosmetics, chemicals, or agriculture, the need for consistent, thorough, and efficient mixing is universal. Poor mixing can lead to product inconsistency, waste, contamination, and loss of valuable resources. To overcome these challenges, companies turn to specialized equipment designed to optimize performance. One such solution that has gained popularity is the conical mixing tank. Its unique geometry and operational benefits make it an ideal choice for efficient liquid processing.
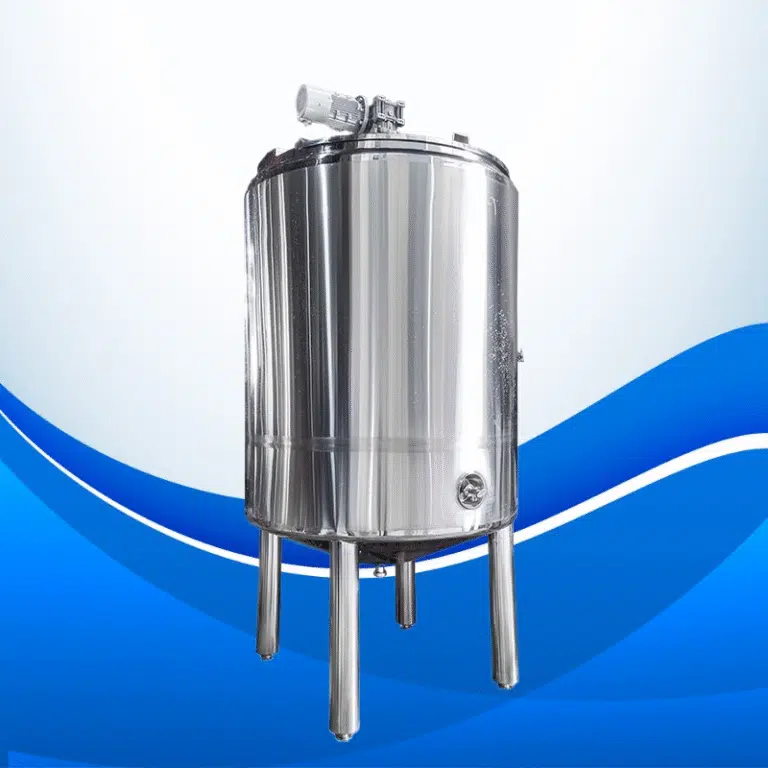
What Sets Conical Mixing Tanks Apart
The defining feature of a conical mixing tank is its cone-shaped bottom, which sets it apart from traditional flat or dished-bottom tanks. This conical design plays a significant role in enhancing the flow dynamics within the tank. When liquids are agitated inside the tank, the shape of the cone helps direct the contents toward the center and downward, allowing for a more thorough and complete mixing process. The natural gravity-assisted flow also simplifies the process of emptying the tank, ensuring that minimal residue remains and reducing the risk of cross-contamination between batches.
Improved Mixing Efficiency
Conical mixing tanks offer superior mixing efficiency compared to conventional tanks. The shape of the cone allows liquids and suspended solids to move in a continuous, vortex-like motion that promotes uniform distribution of ingredients. This is particularly important in industries where the quality and consistency of the mixture directly affect the final product, such as in pharmaceutical compounding or beverage production.
The efficient mixing also reduces the time required to achieve homogeneity, making the overall process faster and more cost-effective. When combined with high-performance mixers or agitators, conical tanks can handle even the most challenging formulations, including those with high viscosity or varying densities.
Enhanced Drainage and Product Recovery
One of the standout advantages of conical mixing tanks is their ability to drain completely and efficiently. Thanks to the steep slope of the conical bottom, gravity naturally drives the liquid toward the central outlet at the lowest point of the tank. This design eliminates the common issue of residual materials sticking to the bottom or corners of the tank, which can occur with flat-bottom models.
Improved drainage means that almost all of the product is recovered, minimizing waste and maximizing yield. This is especially beneficial when working with expensive or sensitive ingredients. In applications where hygiene is critical, such as food or pharmaceutical manufacturing, full drainage also supports easier cleaning and faster turnaround between batches.
Versatility Across Different Industries
Conical mixing tanks are suitable for a wide range of applications due to their adaptable design. In the food industry, they are used to mix sauces, syrups, dairy products, and beverages with consistent texture and flavor. In cosmetics, they help blend lotions, creams, and serums to achieve smooth and stable formulations. In chemical processing, they enable the precise combination of reactive ingredients under controlled conditions.
Their versatility extends to agriculture, where they are used to prepare nutrient solutions and fertilizers, and even in wastewater treatment, where chemicals must be thoroughly mixed before being introduced into the treatment cycle. The same tank design can be customized in size, material, and fittings to suit the specific requirements of each sector.
Ease of Cleaning and Maintenance
Another reason why conical mixing tanks are preferred in liquid processing is their ease of cleaning. The complete drainage capability reduces the need for manual scraping or disassembly. This makes the cleaning process faster, more effective, and less labor-intensive. In sanitary environments, tanks are often fitted with CIP (Clean-in-Place) systems that allow for automated cleaning without the need to open the tank.
Maintenance of conical tanks is also relatively straightforward. With fewer areas for residue buildup and corrosion, the risk of long-term wear and contamination is minimized. Most tanks are built from corrosion-resistant materials such as stainless steel or food-grade plastic, depending on the application. Regular inspection of the mixing equipment, seals, and valves ensures smooth and uninterrupted operation over extended periods.
Energy and Cost Efficiency
Efficiency in liquid processing is not just about speed or performance—it also includes energy use and cost savings. Conical mixing tanks are inherently energy-efficient due to their design. The improved flow dynamics require less power to achieve the same level of mixing compared to flat-bottom tanks. Shorter mixing times and lower energy input translate into reduced operational costs.
In addition, their durability and low maintenance requirements help lower long-term costs. The ability to fully recover the product also reduces material loss, which can be a major source of expense in industries dealing with high-value ingredients.
Design Flexibility and Customization
Manufacturers of conical mixing tanks offer a wide range of customization options to meet diverse processing needs. Depending on the industry, a tank can be fitted with features like temperature control jackets, pressure-resistant walls, sight glasses, sampling ports, and integrated digital controls. Agitators can also be customized based on mixing speed, blade configuration, and power source.
This level of customization allows businesses to optimize the tank’s performance for their specific processes. Whether it’s a batch operation or continuous flow production, conical mixing tanks can be designed to integrate seamlessly into existing systems, improving overall workflow efficiency.
Environmental and Safety Benefits
From an environmental standpoint, conical mixing tanks contribute to cleaner and safer processing. Reduced waste and energy use help lower the carbon footprint of production facilities. The easy-to-clean surfaces and effective drainage also reduce the need for harsh cleaning chemicals, making the operation more eco-friendly.
In terms of safety, the enclosed design and automated features of conical tanks help prevent exposure to hazardous substances. Automated systems can monitor temperature, pressure, and mixing speed, reducing the need for manual intervention and ensuring operator safety during complex mixing operations.
Conclusion
Conical Mixing Tank are an ideal solution for efficient liquid processing across a broad spectrum of industries. Their unique shape and functional design improve mixing quality, reduce processing time, and minimize waste. Whether it's enhanced drainage, easy maintenance, or versatile applications, these tanks offer a range of benefits that contribute to better productivity and cost savings. For any company seeking to optimize their liquid processing capabilities, investing in a conical mixing tank can lead to significant operational advantages and long-term success.